The Fabrication Bays are one of primary components of the Georgia Tech Biocleanroom. Both fabrication bays house UV filter light fixtures in addition to lithography, direct writing, and printing tools.
The direct writing and printing techniques are enabled by computer-controlled two- and three-dimensional pattern formation in a serial fashion. Comparing to other patterning approaches including lithography, and stamping methods, direct write or print based fabrication does not require masks or preexisting patterns, offers versatility to modify fabrication configurations rapidly for proof-of-concept studies and design optimization. In addition, the precise control of material properties with high resolution deposition enable structures that are either impossible or impractical to make with traditional techniques.
Direct Printing Technologies
Jetlab II Ink Jet Printer Bioforce Nano Enabler PiXDRO LP50
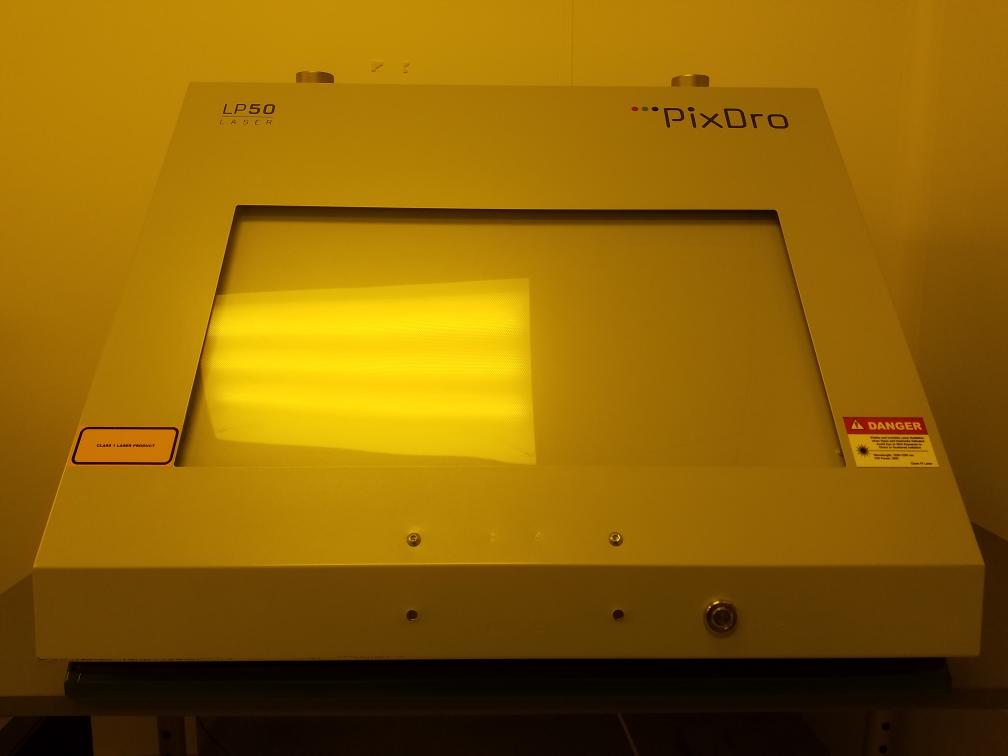
Direct-write Technologies
Nanoscribe
Digital Light Procession Technologies
BMF S140
Through the use of its 405 nm Digital Light Processing system (DLP) large or multiple structures can be printed simultaneously. The S140 has a large build plate and a deep resin vat that make the total print volume 94 mm x 52 mm x 45 mm. These factors make the printer much faster when compared to laser writing systems while still retaining high precision.
While the printer excels at large prints, the S140 can also be used to print small delicate features. The S140 has a 50um resolution in the XY and a 10um (40um max) resolution in the Z. The S140 software allows the user to change layer heights during a print. For example you can start will a 1 mm base with a 40um layer height, then switch to a 10um layer height when your feature is about to print. This makes the system ideal for microfluidic molds, micro needles and rapid prototyping.
Soft Lithography
The Organic Cleanroom houses the Soft lithography Bay. This bay contains equipment specifically designed equipment for Soft Lithography fabrication. Soft lithography is a complementary extension of photolithography and is based on rapid prototyping using negative photoresist SU-8, and on replica molding of poly(dimethylsiloxane) (PDMS) onto the SU-8 film patterned by UV lithography. Due to its unique advantages such as low cost, compatible with large or non-planar surfaces, bio-compatible, etc., it has found its application in many area such as micro-and nanoscale patterning, nano functional devices (OLED, optical transducer, optical waveguide, etc.), and especially in biological researches.
MJB4 Mask Aligner